The IV bag manufacturing process is an important aspect of the medical industry, ensuring safe and efficient delivery of intravenous fluids to patients. With the advancement of technology, the production of infusion bags has evolved to include fully automatic PP bottle infusion production lines, completely changing the manufacturing process.
The fully automatic PP bottle IV solution production line is a comprehensive system, including three sets of equipment: preform/injection machine, bottle blowing machine, and bottle washing-filling-sealing machine. This state-of-the-art production line is designed to streamline the manufacturing process and ensure high efficiency and precision in the production of intravenous infusion plastic bottles.
The IV bag manufacturing process begins with a preform/hanger injection machine, which produces the preforms or hangers used to form the bottles. These preforms are then transferred to a blow molding machine where they are heated and molded into the desired bottle shape. This step is critical to ensure uniformity and quality of IV solution bottles.
Once the bottles are formed, they are transferred to a wash-fill-seal machine, where they go through a series of processes to prepare them for filling with IV fluids. This includes thorough washing to ensure cleanliness and sterility, then precise filling of the IV solution and sealing of the bottle to maintain its integrity.
A major feature of the fully automatic PP bottle large infusion production line is automation, humanization, and intelligent design. This means that the production line is equipped with advanced automation technology, reducing the need for manual intervention and minimizing the risk of errors during manufacturing. Additionally, the system is designed to be user-friendly, with intuitive controls and interfaces that make operation and maintenance quick and easy.
The production line has stable performance and ensures stable and reliable output of high-quality infusion plastic bottles. This stability is critical in the medical industry, where precision and reliability are critical to ensuring the safety and effectiveness of intravenous treatments.
In addition, the fully automatic PP bottle IV solution production line has the characteristics of high production efficiency and low production cost. Streamlined manufacturing processes combined with automated technology enable rapid production of intravenous infusion bottles while minimizing resource waste and operating costs. This makes the line a cost-effective solution for medical facilities and pharmaceutical companies looking to optimize their manufacturing processes.
In short, through the introduction of a fully automatic PP bottle large infusion production line, the manufacturing process of infusion bags has been significantly improved. With its advanced technology, humanized design and high-quality output, this production line has become the first choice for the production of large infusion plastic bottles. Its ability to achieve high productivity and low production costs makes it a valuable asset to the medical industry, ensuring reliable and safe intravenous treatment for patients.
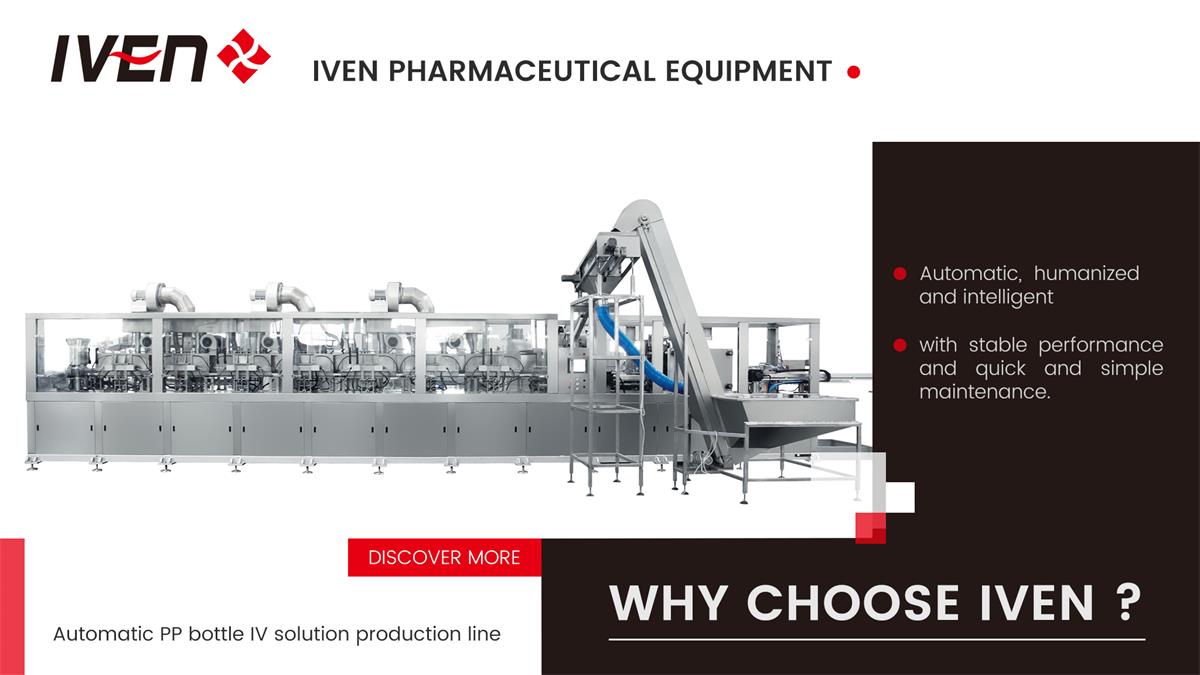
Post time: Aug-16-2024