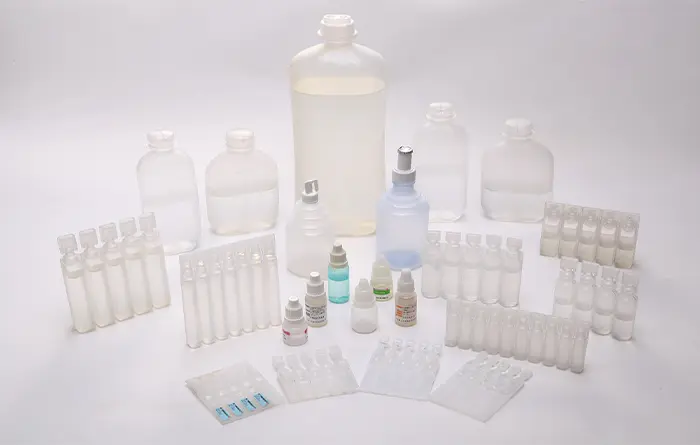
Blow-Fill-Seal (BFS) technology has revolutionized the packaging industry, particularly in the pharmaceutical and healthcare sectors. The BFS production line is a specialized aseptic packaging technology that integrates the blowing, filling, and sealing processes into a single, continuous operation. This innovative manufacturing process has significantly improved the efficiency and safety of packaging various liquid products.
The manufacturing process of Blow-Fill-Seal begins with the Blow-Fill-Seal production line, which adopts specialized aseptic packaging technology. This production line is designed to work continuously, blowing the PE or PP granules to form containers, and then automatically filling and sealing them. The entire process is completed in a quick and continuous manner, ensuring high productivity and efficiency.
The Blow-Fill-Seal production line combines several manufacturing processes into one machine, allowing for the seamless integration of blowing, filling, and sealing processes in a single working station. This integration is achieved under aseptic conditions, ensuring the safety and sterility of the final product. The aseptic environment is crucial, especially in the pharmaceutical and healthcare industries, where product safety and integrity are of utmost importance.
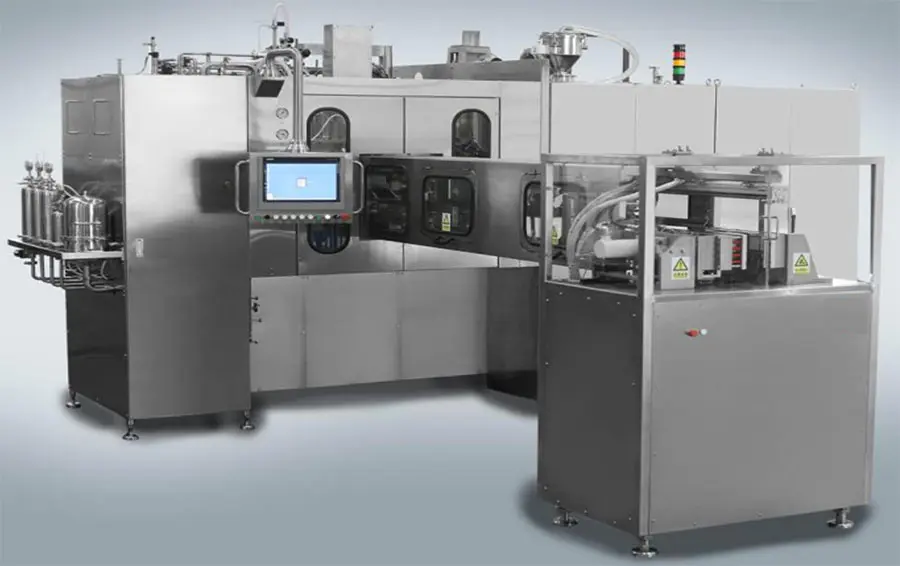
The first step in the manufacturing process of Blow-Fill-Seal involves the blowing of plastic granules to form containers. The production line utilizes advanced technology to blow the granules into the desired container shape, ensuring uniformity and precision. This step is crucial in creating the primary packaging for various liquid products, such as pharmaceutical solutions, ophthalmic products, and respiratory treatments.
Once the containers are formed, the filling process begins. The production line is equipped with automated filling mechanisms that accurately dispense the liquid product into the containers. This precise filling process ensures that each container receives the correct volume of product, eliminating the risk of under or overfilling. The automated nature of the filling process also contributes to the overall efficiency of the manufacturing process.
Following the filling process, the containers are sealed to ensure product integrity and safety. The sealing process is seamlessly integrated into the production line, allowing for the immediate sealing of filled containers. This automated sealing mechanism not only enhances the speed of production but also maintains the aseptic conditions throughout the process, safeguarding the sterility of the final product.
The Blow-Fill-Seal production line’s ability to integrate blowing, filling, and sealing processes in a single operation offers numerous advantages. Firstly, it significantly reduces the risk of contamination, as the entire process takes place within a closed, aseptic environment. This is particularly crucial in industries where product sterility is non-negotiable, such as pharmaceutical manufacturing.
Post time: Jun-19-2024