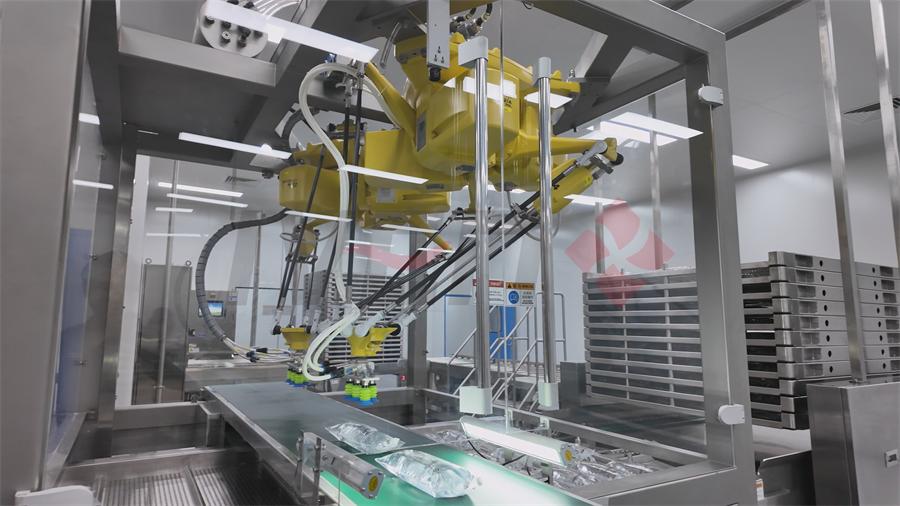
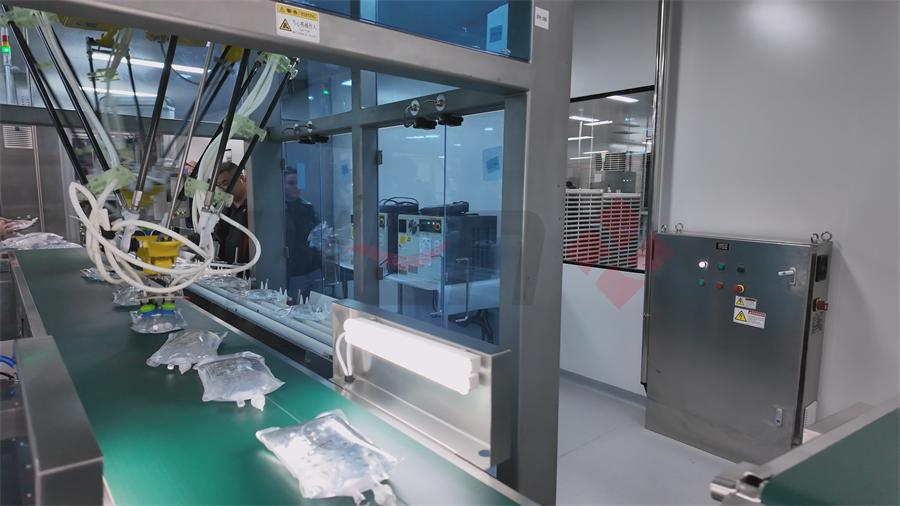
IVEN Pharmatech is honored to have undertaken the turnkey project for the first pharmaceutical factory built by a Chinese company in the United States. This modern soft bag large volume parenteral (LVP) pharmaceutical plant is designed and built in strict compliance with US CGMP standards. It covers a total area of approximately 4,600㎡, with over 3,000㎡ of clean areas, including a 2,300㎡ production workshop, a 924㎡ laboratory, and a 40㎡ sampling room. The plant layout is functionally divided into three major areas: laboratory, production, and auxiliary, each equipped with customized air conditioning systems. The laboratory area is partitioned according to testing needs: positive testing room (AHU-6101/ISO Class 8), microbial limit room (AHU-6102/ISO Class 7), sterile testing room (AHU-6104/ISO Class 7), while the QC physical and chemical area uses comfort air conditioning (AHU-6105). The production area is equipped with specialized clean units according to process characteristics, such as cleaning (AHU-6106/ISO Class 8), material feeding (AHU-6107/ISO Class 7), and core solution preparation and filling (AHU-6109/ISO Class 7). The auxiliary area is equipped with an AHU-6108 air conditioning system.
Key production equipment integrates automation technology: the filling line adopts a fully linked system for printing, bag making, and filling, the solution preparation system achieves CIP/SIP cleaning and sterilization, and is equipped with a high-voltage discharge leak detector and a multi-camera automatic light inspection machine. The downstream packaging line achieves a high-speed operation of 70 bags/minute for 500ml products, integrating 18 processes such as automatic pillow packaging, intelligent palletizing, and online weighing rejection. The water system includes 5T/h pure water preparation, 2T/h distilled water machine, and 500kg pure steam generator, with online monitoring of key parameters such as temperature and TOC.
The plant complies with international standards such as FDA, USP43, ISPE, and ASME BPE, and is validated through the GAMP5 quality management system, forming a full-process quality control system from raw material handling to finished product warehousing, ensuring that the terminally sterilized products with an annual production capacity of 3,000 bags/hour (500ml specification) meet global drug regulatory requirements.
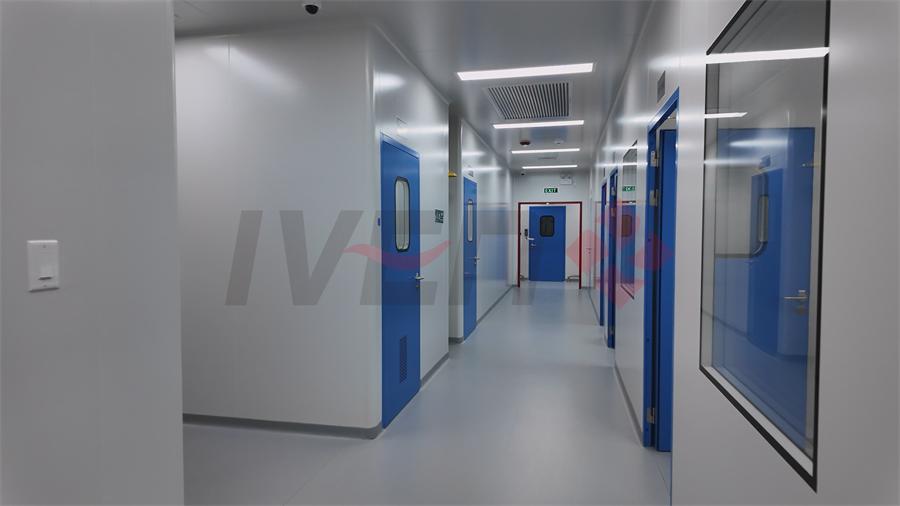
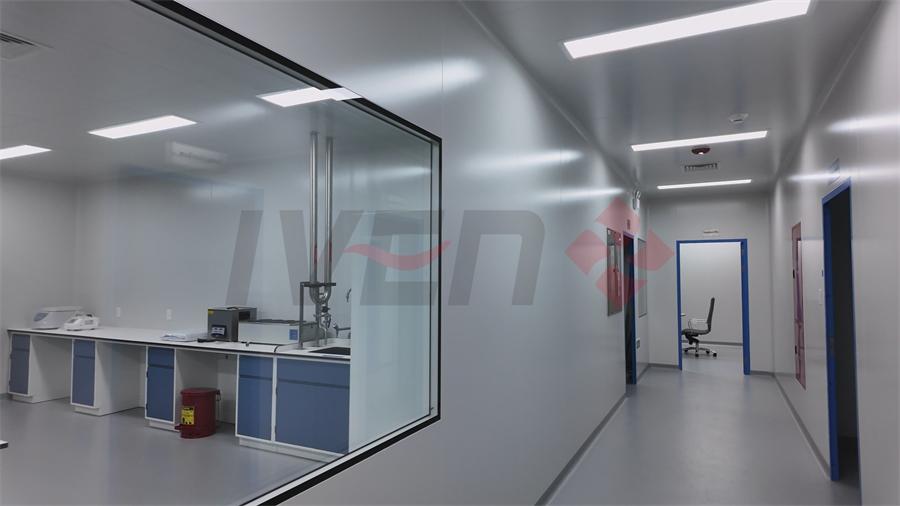
Post time: Feb-27-2025