factory Outlets for Ampoule Leak Testing Machine - Glass Bottle IV Solution Production Line – IVEN
factory Outlets for Ampoule Leak Testing Machine - Glass Bottle IV Solution Production Line – IVEN Detail:
Introduction
Glass bottle IV solution production line is mainly used for IV solution glass bottle of 50-500ml washing, depyrogenation, filling and stoppering, capping. It can be used for the production of glucose, antibiotic, amino acid, fat emulsion, nutrient solution and biological agents and other liquid etc.
Product Video
Step 1
Washing machine:
This machine is used for the fine washing for infusion glass bottle, take turns to use the normal water, purified water, injection water, clean compressed air, fresh injection water and clean compressed air to washing the bottle in turns.
Step 2
Depyrogenation Tunnel
Laminar flow sterilization tunnel used for washed vial’s dry sterilization and remove heat, It can reach the highest temperature 300~350℃, efficient sterilization time for 5-10 minutes.
It has three working area (Preheat area, heating area, cooling area).
Step 3
Filling, Vacuuming, Nitrogen Charging, Stoppering Machine
Filling part adopts Germany GEMU valve filling, high precision.
Nitrogen charging immediately after filling, also nitrogen protection between the nitrogen charging and stoppering.
No bottles no filling, no bottles no vacuuming, no bottle no nitrogen charging, ensure the vacuum level in the air tank during vacuuming, meanwhile, make sure the oxygen residual after stoppering (control within 1.0%)。
Step 4
Filling and Stoppering Machine
Aseptic liquid filling machine is very accurate and stable operation. The filling volume can be directly adjusted through HMI, here we have ORABS equipped with stainless steel laminar air flow hood.
Step 5
Capping Machine
It is mainly used for glass bottles capping. Continuous operation. Picking up and crimping, at the same time rolling the cap. After the completion, the cap have the same size and edge smooth, good appearance. High-speed, low damaged.
Advantages:
1.Separate pipeline for cleaning medium, no cross-contamination, according to GMP requirements.
2.Filling head synchronously tracks filling, high filling accuracy.
3.Adopt full servo drive system, no mechanical transmission.
4.Nitrogen charging function can be configured (before filling, during filling, after filling).
5.Quick changeover time for different bottle size.
Application in hospital:
Technical Specifications:
Filling, Nitrogen Charging, Stoppering Machine
Item |
Machine model | ||||
CNGFS16/10 |
CNGFS24/10 | CNGFS36/20 | CNGFS48/20 | ||
Production capacity | 60-100BPM | 100-150BPM | 150-300BPM | 300-400BPM | |
Applied bottle size | 50ml, 100ml, 250ml, 500ml | ||||
Filling accuracy | ±1.5% | ||||
Compressed air (m³/h) | 0.6Mpa | 1.5 | 3 | 4 | 4.5 |
Power supply | KW | 4 | 4 | 6 | 6 |
Weight | T | 7.5 | 11 | 13.5 | 14 |
Machine size | (L×W×H)(MM) | 2500*1250*2350 | 2500*1520*2350 | 3150*1900*2350 |
3500*2350*2350 |
Product detail pictures:

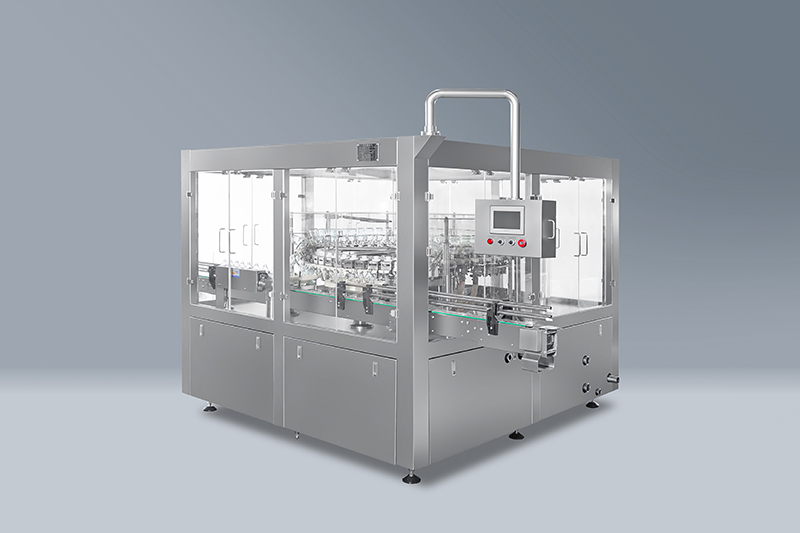

Related Product Guide:
Our commission is to serve our users and clients with best quality and competitive portable digital products for factory Outlets for Ampoule Leak Testing Machine - Glass Bottle IV Solution Production Line – IVEN , The product will supply to all over the world, such as: Cyprus, Guatemala, Ottawa, If you are for any reason unsure which product to select, do not hesitate to contact us and we will be delighted to advise and assist you. This way we will be providing you with all the knowledge needed to make the best choice. Our company strictly follows Survive by good quality, Develop by keeping good credit. operation policy. Welcome all the clients old and new to visit our company and talk about the business. We are looking for more and more customers to create the glorious future.

The company leader recept us warmly, through a meticulous and thorough discussion, we signed a purchase order. Hope to cooperate smoothly
